This post contains affiliate links, which means I may earn a small commission at no cost to you if you make a purchase through my link. Information provided for educational purposes only. Please consult experts and professionals before taking action on the below.
Consider sponsoring this post to help us share this knowledge with others!
Introduction: Why Factory Layout Matters
A well-designed factory layout is essential for boosting productivity, reducing inefficiencies, and streamlining operations. By strategically organizing workstations, machinery, and materials, manufacturers can:
- Enhance workflow efficiency
- Minimize waste and downtime
- Improve worker safety and comfort
- Reduce operational costs
In this guide, we’ll explore key strategies for optimizing factory layouts to maximize productivity and support long-term business success.
1. Analyzing Workflow for Maximum Efficiency
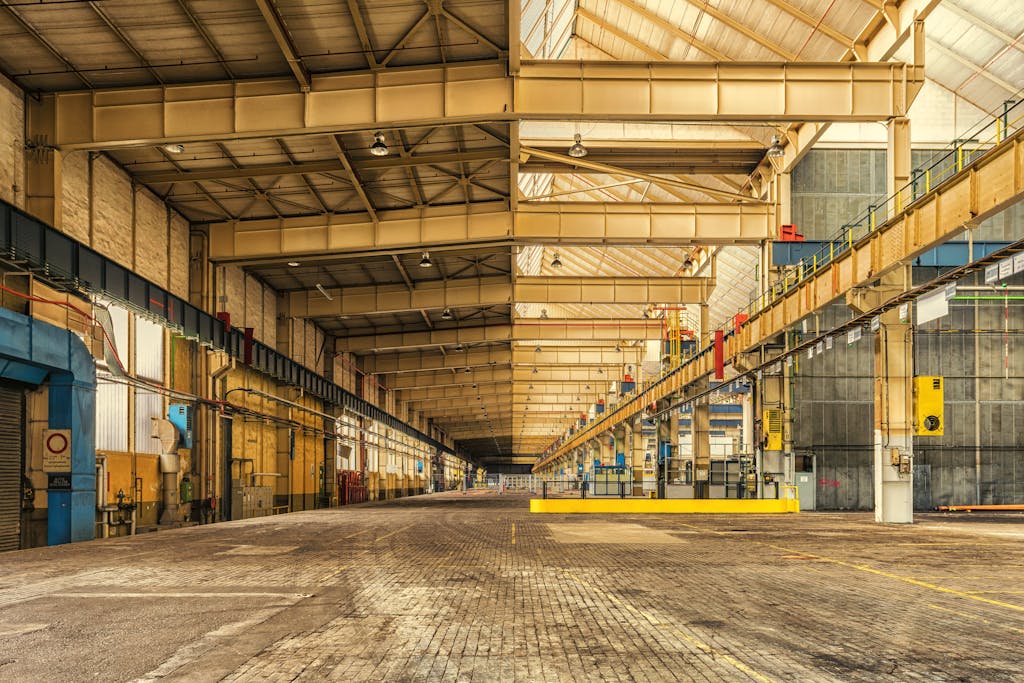
The first step in factory layout optimization is analyzing the flow of materials and workers. A disorganized factory floor leads to:
- Wasted time due to unnecessary movement
- Production bottlenecks that slow output
- Higher labor costs from inefficiencies
Best Practices for Workflow Optimization
✔ Map out the current workflow and identify areas where movement can be minimized.
✔ Arrange workstations in a logical sequence to create a continuous production flow.
✔ Reduce backtracking by ensuring that raw materials move seamlessly through each production stage.
2. Strategic Equipment & Machinery Placement
Placing machines and workstations in the right locations is crucial for reducing transport time, improving efficiency, and lowering costs.
Key Considerations for Machinery Layout
- Position related machines close together to minimize movement between tasks.
- Ensure maintenance areas are easily accessible to reduce downtime from equipment repairs.
- Incorporate lean manufacturing principles, such as 5S methodology, to keep workspaces tidy and functional.
3. The Role of Ergonomics in Factory Design
An optimized factory layout isn’t just about machinery—it also affects worker comfort and efficiency. Poor ergonomics can lead to:
- Worker fatigue
- Increased error rates
- Higher injury risks
- Reduced productivity over time
How to Improve Workplace Ergonomics
✔ Provide adjustable workstations to accommodate workers of different heights.
✔ Ensure sufficient space for movement to prevent strain.
✔ Invest in anti-fatigue flooring and ergonomic seating for long-standing workstations.
4. Adapting Factory Layouts for Growth & Technology
A factory layout should be flexible enough to accommodate:
- New technologies and automation
- Business growth and expansion
- Changing production needs
Best Practices for Long-Term Adaptability
✔ Use modular layouts that can be easily reconfigured.
✔ Regularly review workflow and make adjustments based on performance metrics.
✔ Invest in scalable infrastructure to prevent disruptions as demand increases.
Final Thoughts: The Key to a High-Performance Factory
By focusing on workflow optimization, strategic equipment placement, ergonomic design, and flexibility, manufacturers can maximize efficiency, reduce costs, and support long-term success. A well-optimized factory layout is not just an investment in productivity—it’s a competitive advantage.
Leave a Reply